Surely you have read the term Lean PPM™ a few times on this blog already. Today I examine one aspect of ‘”Lean” in the context of project portfolio management: waste.
But first things first:
Lean management is an outgrowth of the Toyota Production System (TPS) and consists of a collection of technologies, attitudes, and processes for the development and production of industrial goods. It started in Japan after the end of World War II and achieved worldwide recognition in the 1980s (Womack, James P. / Jones, Daniel T. / Roos, Daniel: The machine that changed the world. How Japan’s secret weapon in the global auto wars will revolutionize Western industry, New York: Harper Perennial (1991)). There are several key elements of lean, including
- The focus on man as the key element of production
- The creation of a consistent production flow
- The continuous improvement of quality
- The shifting of decision-making power to the lowest level
- The inclusion of customers and suppliers
In this article, I would like to focus on one more key item: the creation of “value.” It is precisely this focus that has finally carried the concept of lean far beyond the production floor (Hines, Peter/Holweg,Matthias / Rich, Nick: Learning to evolve: A review of contemporary lean thinking in: International Journal of Operations & Production Management 2004 24:10, pp. 994-1011).
What is “Value?”
Lean defines value as something a customer is willing to spend money on.
As you can see, this is a very subjective definition from the perspective of your potential customers. Not to mention time dependent: a characteristic that seems indispensable today can be completely worthless tomorrow.
Lean goes further and explains the necessity of performing only those activities that increase the value of your product. This sounds simplistic, of course, but is not so easy in practice. Think about it: is it value-creating to order a few more parts than needed because your supplier will then give you a much better price? Try it once the other way around, like lean, and take a look at the reverse. Lean calls non-value-creating activities “muda,” or waste. This waste can occur in seven different forms:
- Unnecessary transportation
- Excessive inventory
- Unnecessary motion
- Waiting
- Overproduction
- Overprocessing
- Defects
Therefore, a value-creating activity is one that causes no waste (and ordering an unnecessary quantity of parts would thus be a waste in terms of inventory).
Let’s Apply this to PPM
Now it gets interesting: the seven forms of waste have already been applied to other disciplines, such as software development (For example, compare Poppendieck, Mary/Poppendieck, Tom: Implementing lean software development. From concept to cash, Upper Saddle River: Addison-Wesley (2007)) and logistics (Hines, Peter/Holweg, Matthias/Rich, Nick: Lean logistics in: International Journal of Physical Distribution & Logistics Management 1997 27:3/4, pp. 153-173). In this brief article, we examine the project portfolio management environment in terms of the seven forms of waste, and we reflect on whether avoiding them could also increase the “value” of the portfolio for the customer.
1. Unnecessary Transportation
- Short-term decision to externalize projects due to limited internal resources.
- Equally short-term recall of outsourced projects due to modified priorities.
- Time modifications and the resultant replanning.
2. Excessive Inventory
- Too long a list of projects to be implemented, which will probably never be approved.
- Inclusion of projects in programs, when such projects are suitable in terms of the resource/budget/know-how situation but are not important.
- Implementation of projects based on the belief that the functionality/products will certainly be needed later, even though the necessity does not exist.
3. Unnecessary Motion
- Spreading employees across too many projects at the same time, and the associated major loss of efficiency due to jumping back and forth.
- Detailed planning of projects that will not be implemented until later.
- Unnecessary coordination activities to transport information to locations where it is not needed.
- Fetching/explaining/onboarding: this should not be necessary when decisions are made where the information is already present.
- Stubborn adherence to formalities for mini-projects or projects whose implementation is clear-cut anyway.
4. Waiting
- Resource constraints
- Waiting times to cover resource constraints
- Insufficient budget
- Shifting decisions along the planning calendar
5. Overproduction
- Implementing projects because there is still money available.
- Forcing through projects outside of the prioritization process.
6. Overprocessing
- Question-raising, labor-intensive project evaluations based on lists of issues that have nothing to do with the reality of a department.
- Requests for highly detailed justifications for projects, and central evaluations in a PMO, that cannot trace the real necessity for the individual departments.
- Preparation of unnecessary business cases for projects without recognizable deposits, in order to calculate a net present value.
- Detailed preparation of project plans for the automatic optimization of the resource situation.
- Calculation of an efficient frontier for the automatic selection of the right projects.
7. Defects
- Selecting the wrong projects despite complex processes
- Putting together a portfolio that results in resource constraints
- Exceeding budgets
- Selecting projects that are contradictory in content
- Selecting projects that do not fit together in terms of their sequence
Already Experienced
The list presented here is a small selection of all project portfolio difficulties and only highlights the “hair in the soup.”
However, it is important to note here that you should always be aiming to establish a method of project portfolio management that avoids every form of waste. A PPM method characterized by
- Organizational anchoring of responsibilities
- Decentralization of decisions
- Short, fast, traceable processes
Why? Because avoiding waste leads to the creation of value. Value that your customer is willing to spend money on now.
Read Next
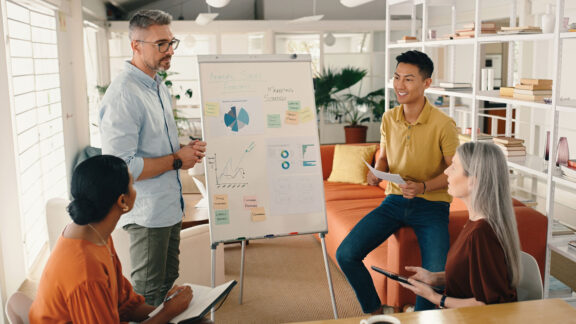
Data Quality: The Achilles Heel of Project Portfolio Management
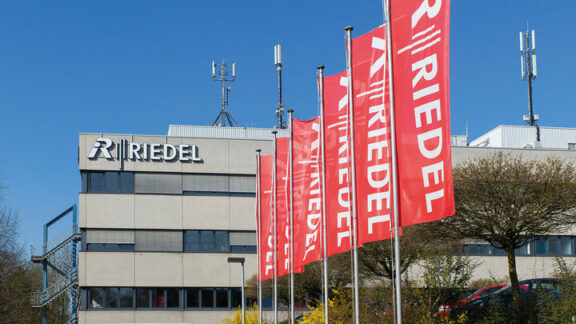