As in my last post, The Fractal Organization, I would again like to take a more constructive view in this article and put forth suggestions for lean project portfolio management. Based on a brief description of lean production, I will explain what lean project portfolio management means and what effects it can have on your organization.
Why Lean?
Why lean? Isn’t this concept already a bit overwrought, and hasn’t it been connected with too many topics of late? Isn’t lean just another fad that will run its course, only to be replaced by the next great thing (agile? teal?) in short order? In my opinion, the answer here is a clear “no” based on the 70-year success story of lean as well as the enormous appeal it has developed throughout the automotive industry and beyond.
Agile Project Management has its Roots in Lean Production
Interestingly, even the great triumph of agile software development can largely be traced back to its originators’ preoccupation with the basic features of lean (Compare Leute, Jörg (2014): Eine neue Definition agilen Projektmanagement [A new definition of agile project management], Wiesbaden, Eul Verlag). Lean methods such as pull, flow, quality management, team emphasis, customer integration, and waste avoidance are clearly attributable to lean and its tenets.
Lean? What Does that Mean Exactly?
The term “lean” traces back to James Womack and Daniel Jones, who studied Japanese automotive companies, especially Toyota, at the end of the 1980s and found the basis for efficiency, quality, and cost efficiency in the production methods used. The authors of “The machine that changed the world” coined the term “lean production” to describe the intensive cost optimization and avoidance of every type of waste in the Toyota production system (Womack, James P. / Jones, Daniel T. / Roos, Daniel: The machine that changed the world. How Japan’s secret weapon in the global auto wars will revolutionize Western industry, New York: Harper Perennial, 1991).
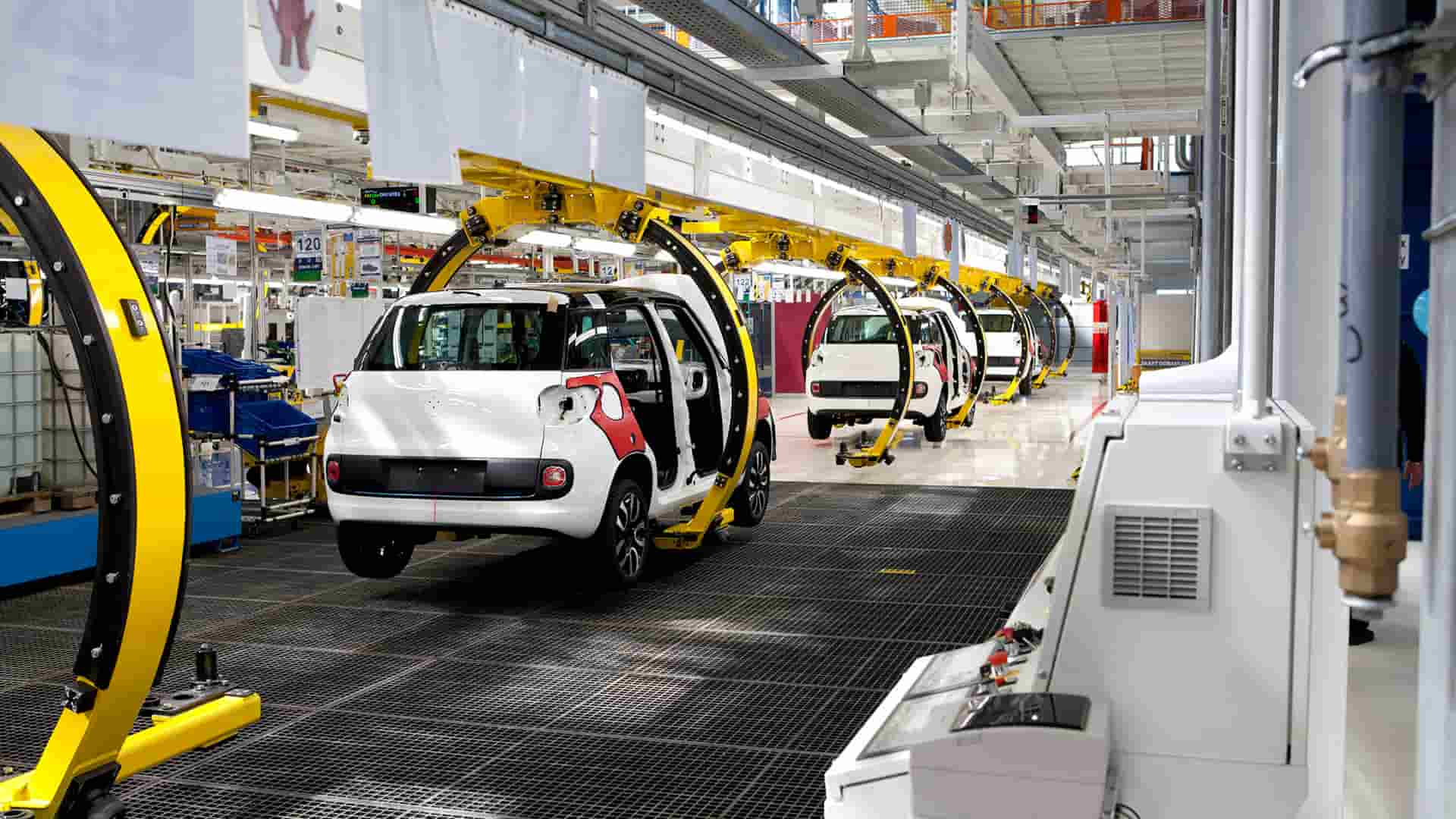
Constraints and the Fractal Organization
As you have probably already gathered, the lean project portfolio management approach that I am presenting here goes somewhat beyond a simple collection of methods for the PMO or the PPM team. Lean PPM means that the organization must change. One of the core problems of traditional PPM is ultimately being at the mercy of the utilization and overloading of constraints.
A wide variety of approaches have been discussed in recent years to avoid constraints. One prominent example is the “Theory of Constraints,” which provides techniques for identifying and dealing with constraints. Now, as we finally get to the heart of the matter, we need to remember two things:
- Every system has a constraint. No matter how you design it, every system will have a limiting factor somewhere. Even if your “machine” runs perfectly, you will have a constraint: your sales. The Theory of Constraints seeks out this constraint specifically, protects it from incidental fluctuations, and coordinates supplies in order to utilize it to capacity.
- Even if you find a constraint and expand to eliminate it, the next constraint will appear; and the next, and the next, and so on. The more complex your system, the more constraints you will have.
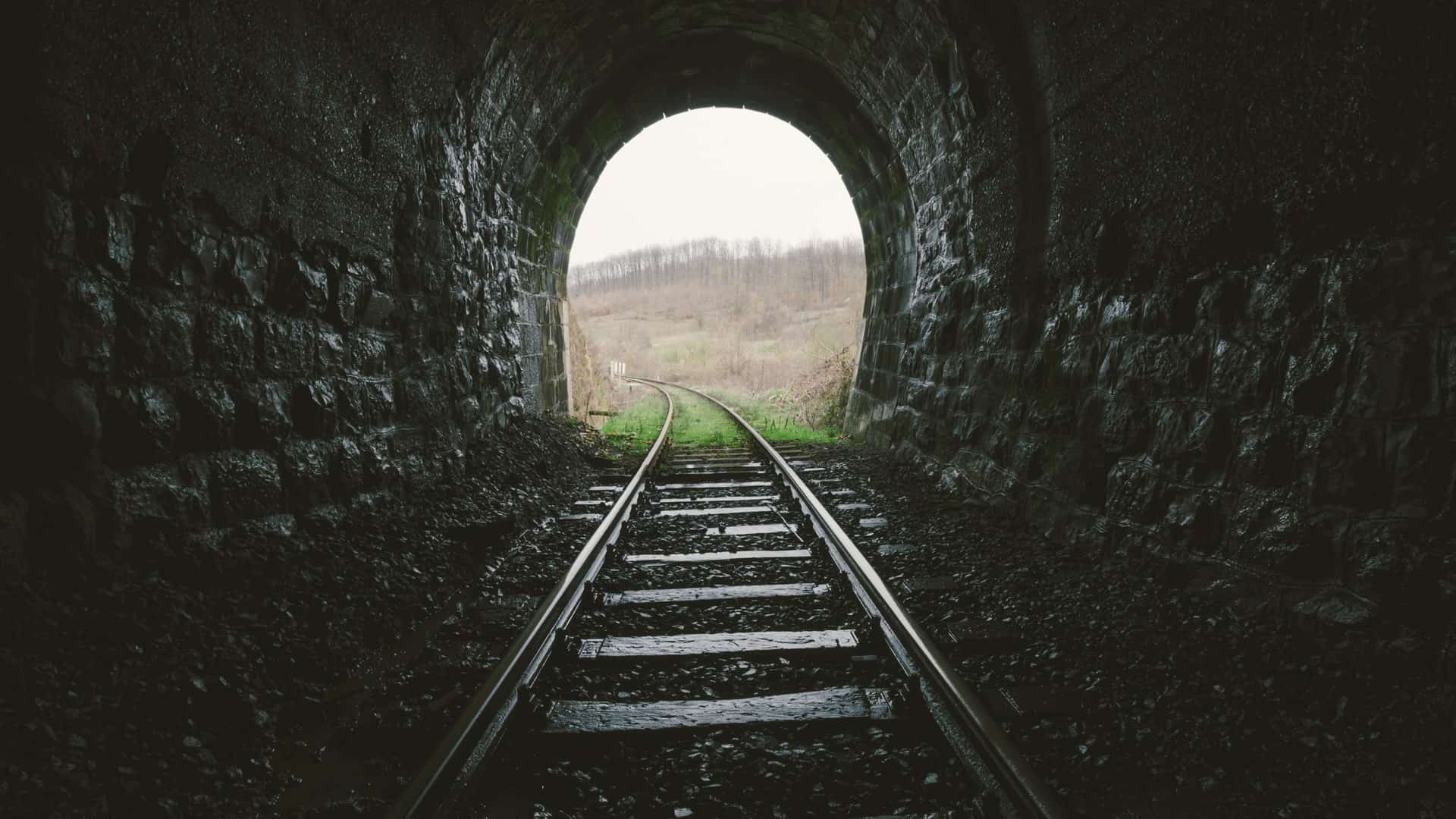
Core Elements of Lean
What do we learn from this? Wouldn’t it be better to establish a system that, in and of itself, has as few constraints as possible and makes your life easier in terms of searching, optimizing, and coordinating? In this article, I build on my suggestions regarding fractal organization and take a closer look at what tasks exist for a “system,” meaning a specialist department, a team, or a group. I also contemplate what sets lean apart and whether the use of PPM results in approaches that counteract the problems of traditional PPM. So let’s start by identifying important, core elements of lean:
- Lean thinks in teams. The team is the central element of all value creation and is responsible for production, quality, and improvement. The importance of the team is evident in the “upside down” responsibility of a production step: the team, not management, decides on a production step. Or, as expressed by lean: decisions are always made by the instance with the most information.
- Focus on the value. The question is always asked, whether an action or a result is considered by the customer to represent a subjective value for which the customer would spend money.
- Pull: the pace of production is not determined by the conveyor belt; teams “pull” work as soon as they are finished with their current work. This prevents overloading.
- Pallet size 1: the ideal in lean is not to prepare pallets of goods and transport them from A to B, but always to transport a workpiece individually. This ensures maximum flexibility for the customer and provides the perfect conditions for pull and flow.
- In addition to customers, suppliers are also integrated in the production network. They help determine the production process and can provide early feedback on the feasibility of a desired step.
- Lean production recognizes seven different forms of waste (muda) such as rework, unnecessary transportation, etc. Consequently, there are various methods provided to root it out. The objective is to avoid waste of every kind.
Applying Lean to PPM: Lean Project Portfolio Management
1. Teams
Interestingly, lean management represents exactly what we have already seen in complex systems: non-interference in the work of the team. Lean is based on the notion that the person with the most information makes decisions, not the person with the greatest power. In other words, the person on the line, not a previously defined process, decides how and in what manner to tighten screws. Suggestions are recorded, discussed, and implemented in periodic quality circles.
2. Focus on Value
Precisely due to time dependencies (what is the customer willing to pay money for now), it is not ideal to create long lists of project priorities in one go, but rather to use simple lists. Record all projects to be implemented and sort them by hand. Ask yourself and other people with an overview: which project is more important here, what dependencies are there? Do this periodically. Set up the portfolio committee as an agile team that prioritizes projects instead of “user stories.”
Interestingly, this can also result in an increased need for money or resources: if it becomes clear that current resources are not enough, this can be a perfect opportunity to quickly expand capacities and integrate them in the team. The question at this point is not whether the necessary tasks fit within the budget, but whether the potentially achievable value contribution justifies the expense.
3. Pull
As soon as a project team has finished a project or a project substep, it can pull the next project exactly when the team is once again available; not according to a predetermined plan. This can, of course, also be when the portfolio committee has decided to end a project early.
Because such projects flow consistently through the system, the teams are permanently utilized to capacity, but not overloaded. The teams themselves decide who will work on what, and in what order. As a result, the members are utilized to capacity and do not need to waste time waiting through an excessive buffer until the next milestone, or work all night due to poor estimates. If you don’t want to do away with detailed, predetermined planning, it could be worthwhile to take a look at critical chain project management (Goldratt, Eliyahu M (1997): Critical chain. Great Barrington: The North River Press).
4. Pallet Size 1
The minimum pallet size, applied to PPM, consists in providing results as quickly as possible. This means that the review cycles between client and contractor should be kept as short as possible. Pallet size 1 is best approximated when, as in a kanban system, cycles no longer exist, but rather a result is delivered exactly when it is ready. Consequently, this means that there are no more milestones, planning calendars, or large cycles in the organization; instead, everything is processed as quickly as possible without overloading people.
5. Integration of Suppliers
Treat external companies and employees as real members of your organization. Be prompt about making decisions regarding the integration of external resources. This will minimize friction in the event of short-term resource increases. Additionally, think in the long term about the development of your organization and the need for skills in the future. This will help you make prompt decisions about expanding or about opening additional locations.
6. Avoid Waste
As I have already highlighted the seven forms of waste in another blog article, I will only briefly mention that lean emphasizes the avoidance of waste to such an extent because all activities that are not wasteful create value.
Will It Keep Going? Yes.
As previously noted in the context of “kanban,” your organization should ideally implement the steady value-creation “flow” desired in lean. This can succeed if this steady creation is applied consistently from the smallest team up to the highest level. It is important to couple steady delivery of value with a simultaneous ability to respond to changing priorities. This is exactly what agile methods such as scrum and “kanban” offer. At the same time, they represent a major change for large organizations, especially when the introduction doesn’t end with the “lowest” teams and middle management has to say good-bye to the peace of fixed budgets, clear planning cycles, and long phases. Constant review, adjustment, and communication are prerequisites for a truly lean organization.
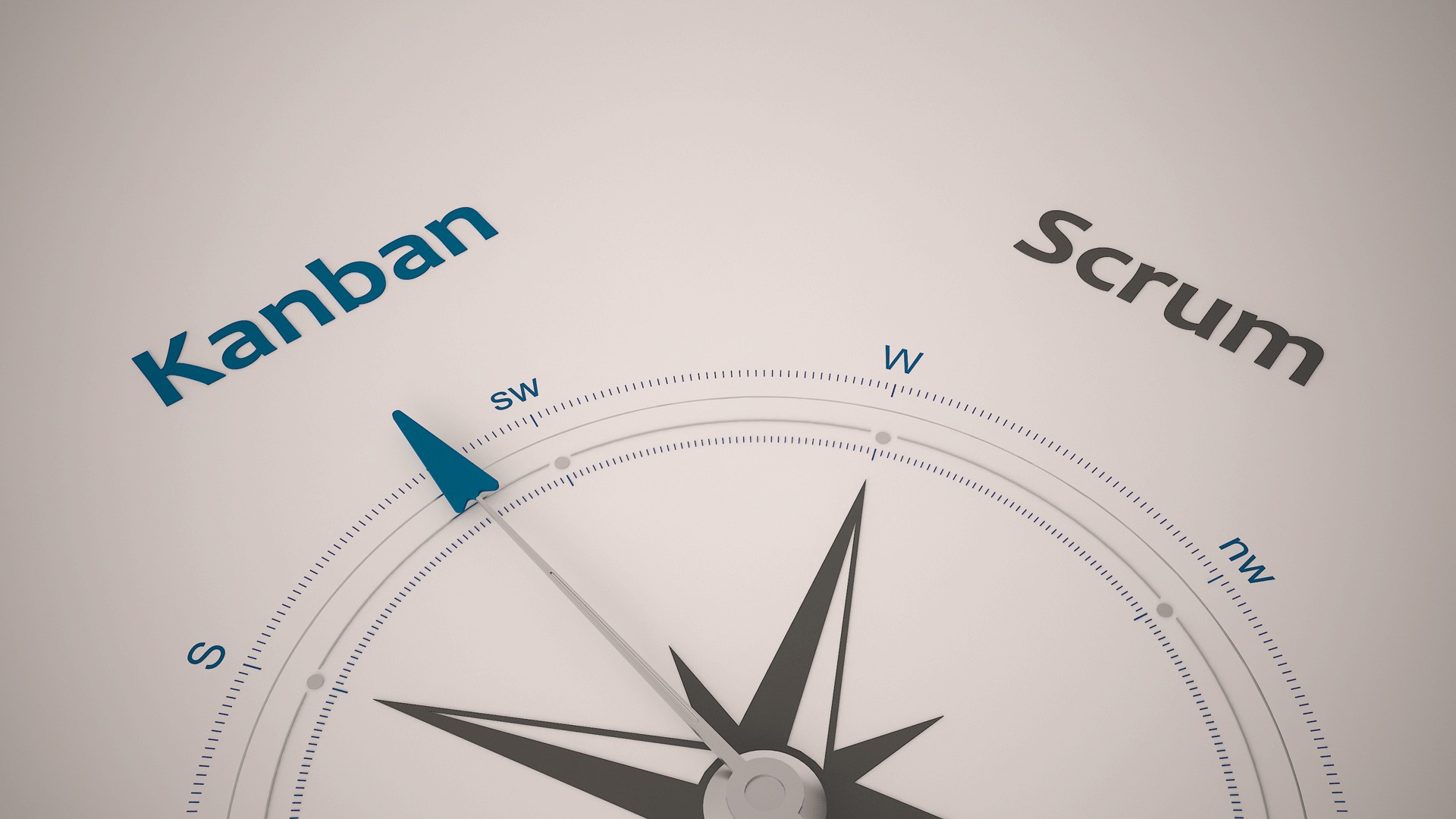
Rome Wasn’t Built in a Day
Now this might sound like a lot to do all at once. Don’t worry, you don’t have to introduce everything at the same time. It is advisable to proceed in the following order:
- Prioritize existing projects more frequently than once per year.
- Make project dependencies clear and be mindful of them.
- Assemble interdisciplinary teams.
- Reduce multitasking.
- Reduce project cycle times; introduce the shortest possible timeboxes.
For all steps, always consider the involvement of project managers, team leaders, and the shop council (where experience has shown that the latter will support rather than torpedo your initiatives).
Thanks to the Lean PPM approach with its corresponding reporting, we are now able to efficiently manage even complex and interdisciplinary projects. The standardized database enables us to conduct more targeted reviews of completed projects and will lead to better and more sustainable project results.
PERI SE
Read Next
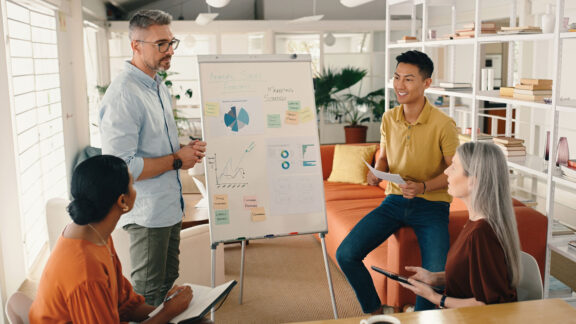
Data Quality: The Achilles Heel of Project Portfolio Management
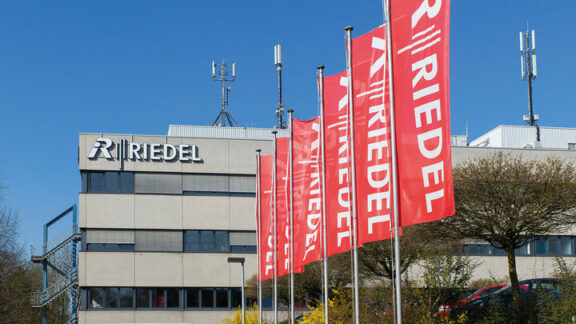