Founded in 1921, Balluff GmbH has grown into a leading global player in sensor manufacturing and is represented in 68 countries worldwide, which presents a big challenge for project portfolio management.
However, Annalena Bergen and Rainer Grundmann and the Project and Process Management team solves this challenge by significantly streamlining processes and using Meisterplan. Balluff has successfully transferred its fairly static processes into a streamlined, dynamic and successful PPM process. The decisive factor in this success was the involvement of all process-involved colleagues, a high level of transparency in the processes and the establishment of regular meetings within the PPM process in order to be able to constantly evaluate and improve it. You can read how this works in this case study.
The Challenge
Like many other companies, Balluff’s IT department had previously adhered to a static project portfolio management process. The project portfolio was planned once a year and then not adjusted further throughout the year.
In addition to the lack of transparency, a major problem was that new topics either had to wait or were done “on the side”, and once planned, projects could not be adapted to changing circumstances.
In 2016, Balluff GmbH decided to revise their PPM process. When searching for a new, simple tool for project portfolio management, the company received a tip from the German Association for Project Management (GPM) : try Meisterplan. After an extensive test phase and regular interaction with Meisterplan experts, Balluff GmbH decided to implement the tool and streamline their existing processes and map them in Meisterplan.
Balluff is a classic use case for Meisterplan’s Lean PPM™ approach. Ultimately, it’s about getting an answer to the question “Who is working on which project, at any given time?”. Meisterplan answers this question. It shows all important information in order to make informed decisions and plan a realistic project portfolio. Information that is not relevant for this purpose is specifically hidden. The result is an overview of the project portfolio, in which resource bottlenecks can be easily identified and resolved.
“The annual planning cycle simply did not work for our reality and the dynamic requirements in our company. There were numerous projects under water and the planning for hardly any project was current and transparent.”
– Rainer Grundmann, Balluff GmbH
The Solution
The Lean PPM™ approach served as the basis for the process optimization that Balluff carried out. In individual discussions with the area and project managers, needs and responsibilities were identified and a lean process was developed together. This process was regularly evaluated and adapted in joint retrospective meetings. Since all those involved in the process were involved in the change management process right from the start, everyone was able to identify well with the process and gladly contributed the necessary changes. The necessary meetings and procedures for successful PPM could therefore be established without many problems. The approximately 20 project managers are involved in the entire PPM process and carry out a monthly update of the cost and capacity planning for the following 3 months. The division heads meet monthly in the Steering Committee and make decisions that affect the portfolio. Team leaders and PMOs solve conflicts together.
The Results
By adapting the Lean PPM™ process with Meisterplan, Balluff was able to significantly increase the visibility of resource conflicts, leading to an early discussion on prioritization and utilization. This also improved the efficiency of their individual projects and enabled more projects to be successfully completed.
Read Next
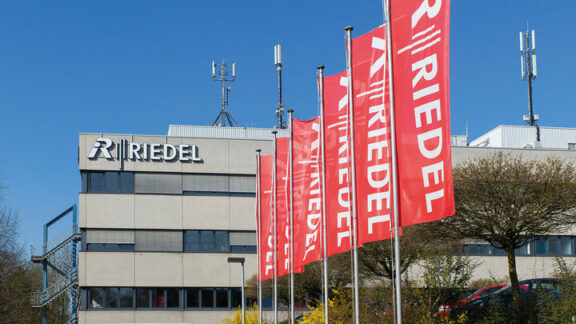
Riedel Conquers Hybrid R&D Projects with Meisterplan’s Strategic Resource Planning
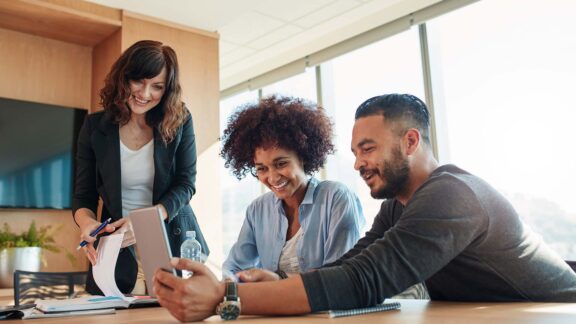